Airtightness and Heat Recovery Systems
- Home /
- Airtightness and Heat Recovery Systems
How airtight does my building need to be for a Heat Recovery Systems to be effective and a good investment?
Airtightness test
Leakage of air through building fabric cannot ensure continuous and adequate ventilation to maintain indoor air quality in occupied buildings. Some new buildings with increased airtightness show the effects of this (dampness and mould), and the less visible effect of high CO2 concentrations.
Air pressure test
The air pressure test (or blower door as it is colloquially known) measures the total leakage through the building envelope (n50-value). This describes the air changes at a differential pressure of 50 Pa. A differential pressure of 50 Pa is created between the inside of the building and the outside by means of a blower door test. The blower door consists of a fan fitted into an opening in the envelope (e.g. a door) creating under pressure inside the building in order to detect leakage. The actual test involves a series of under pressure and overpressure measurements determining the leakage rate at a differential pressure of 50 Pa in relation to the overall building volume. Blower door tests are offered by accredited suppliers.
An air pressure test is essential for Passive Houses - it is part of the certification procedure.
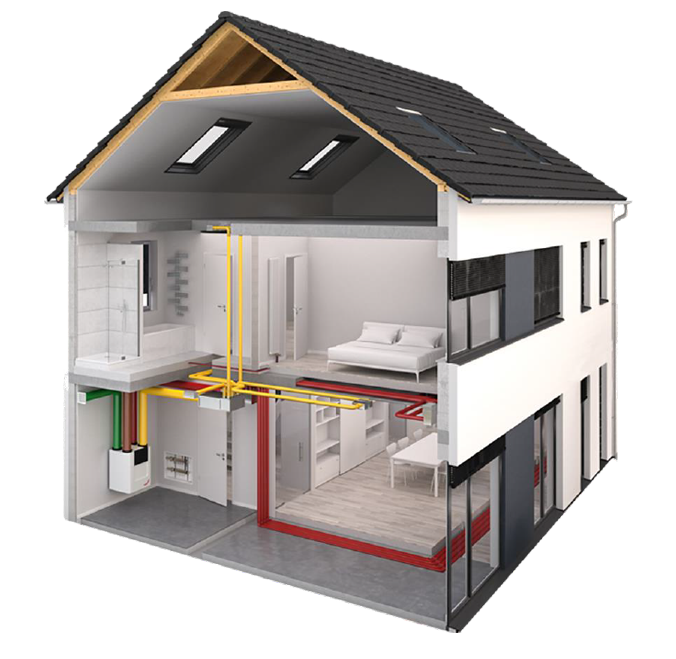
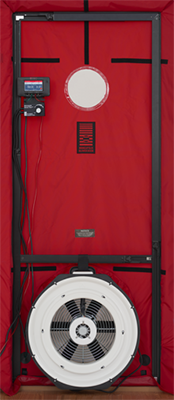
Blower door test
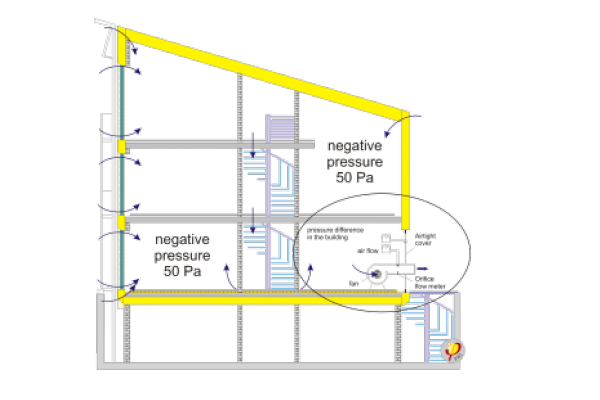
Possible leakage that occurs during testing
Air pressure test
Low leakage values are needed for Passive Houses (n50 leakage rates may not be greater than 0.6 h-1 to comply with the certification criteria). In fact, values between 0.2 and 0,6 h-1 were achieved with built Passive Houses.
Australian Building Air Tightness Database:
The Air Infiltration and Ventilation Association of Australia Inc. (“AIVAA”) has been established to provide collaborative information on current energy rating systems: www.aivaa.asn.au/action/national-database/
To provide context on what these ACH rates mean:
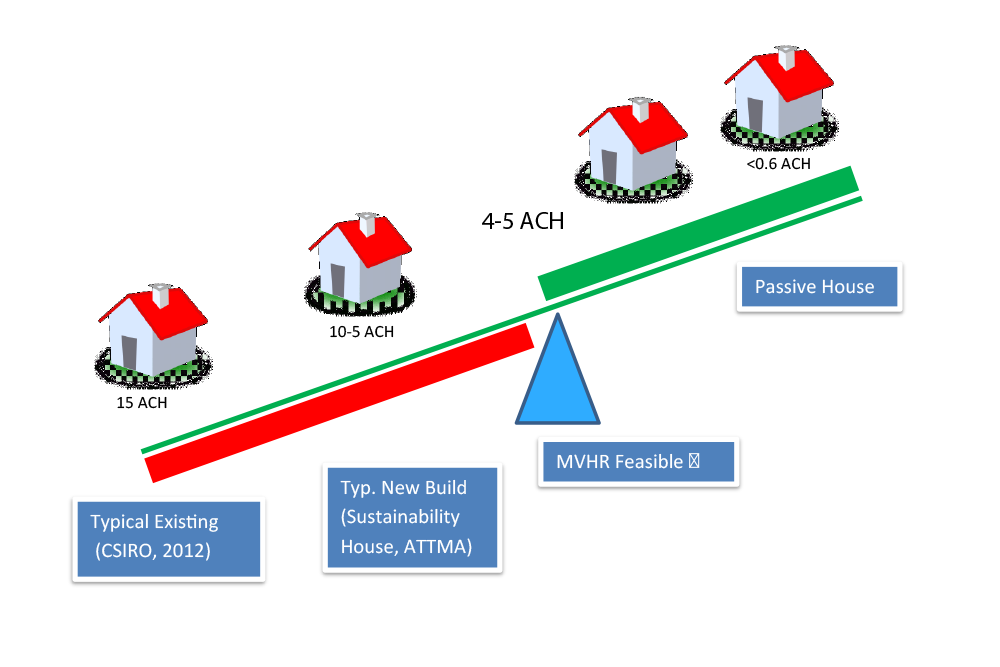
Why isn’t MVHR feasible for less air tight buildings?
MVHR systems typically deliver ~0.35ACH/hr in normal operation. When a typical existing building (with 10 ACH/hr @ 50 Pa) experiences a 35 km/h wind (~50Pa) then approximately 2 ACH/hr of uncontrolled air infiltration is likely to occur.
2 ACH v’s 0.35 ACH doesn’t make sense!
General principles for improving airtightness (excerpt from Passipedia)
The key principle for planning the airtightness of a building is that of the “continuous uninterrupted airtight building envelope”, that can be outlined using the “red pencil method” (see the following illustration). It should be possible to trace the whole building envelope with a pencil without any breaks in each sectional drawing. In the details it must be made clear how the airtight connection is realised. This makes it clear that airtightness is primarily a planning task. Craftsman can only carry this out in an airtight manner if it has been thoroughly designed.
It is essential that only a single airtight layer is planned and implemented. Two “nearly” airtight layers will serve no purpose – leakage will still take place! This can be visualised, for example, by a leakage in the entrance door of a house, where a leaking door in the lobby won’t remedy the problem, or two buckets, both with a hole in the bottom; if one is placed inside the other, this won’t stop the water from leaking out!
It is essential that the concept for airtightness is designed and applied for the long term.
Planning stages for airtightness:
- For each external building component, the component which will form the airtight layer should be specified (e.g. the OSB board or sheeting in a roof construction, the interior plaster for a brick wall, the concrete ceiling between the basement and the ground floor,…). The position of this airtight layer should be shown as a red line in the sectional drawing or floor plan. The heated space must be completely enclosed by the airtight layer.
- As a second step, it must be specified how the ends of the airtight component layers will be permanently and airtightly joined. Attention: it is not enough to “connect” the window frame to the brick wall, for example, (because the wall level is not airtight!). Instead, the window frame must be permanently joined with the airtight layer of the external wall, which is usually the interior plaster in a solid construction, for example. For this example, it would be suitable to use tape that can be plastered over, or a plastering strip.
- Thirdly, any necessary penetrations must be planned : electric cables and pipelines which pass through the basement ceiling, power sockets (!) in external walls, etc.. Today suitable tried and tested solutions and materials are available for this purpose. However, the principle of avoidance should be applied at first: it should be checked whether the penetration really is necessary.
Source Passipedia. 2017. The Passive House Resource. [ONLINE] https://passipedia.org/planning/airtight_construction/ general_principles/principles_for_improving_airtightness
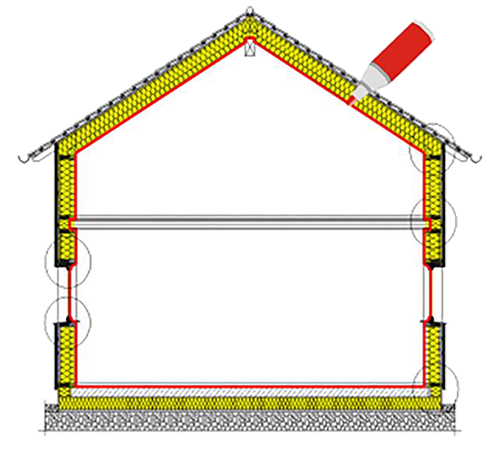
Details are important – but what is more important is the basic concept. A building envelope can only be airtight if it consists of just one uninterrupted airtight envelope enclosing the whole conditioned space (red line).
About Us
Fantech, the industry leader for 45 years and continues to be the forefront of fan and acoustics technology by developing and implementing new and innovative products for virtually every air movement and ventilation need.